The transportation industry grew tremendously over the last decade because people have been traveling a lot more. Trains are becoming an attractive way of traveling because they are matching perfectly the necessity to have low carbon emission means of transportation. With increases in infrastructures and the growing number of vehicles in circulation, all rails safety related topics are one of the top priority. Railway industry is using lots of different methods to control, maintain, and prevent hazards, this article will focus in the use of Ultrasonic for Rail flaw detection. Nowadays most of companies providing Ultrasonic Rail flaw detection are using conventional ultrasound avoiding Phased Array Ultrasonic Testing (PAUT) due to a lack of knowledge and application constraints. What would you say if you could replace several conventional probes by one phased array transducer reaching the same probability of detection if not better?
FAAST-PA is a worldwide patented phased array able to generate multiple ultrasonic beams at different angles in one shot. It removes PAUT technical constraints for Ultrasonic testing of railway track at low and high-speed and add some benefits compare to conventional ultrasonic.
This article will compare probability of detection between conventional probes and FAAST-PA. Hereunder is the rail sample used for trials which has different kind of defects with different sizes, shapes and depth.
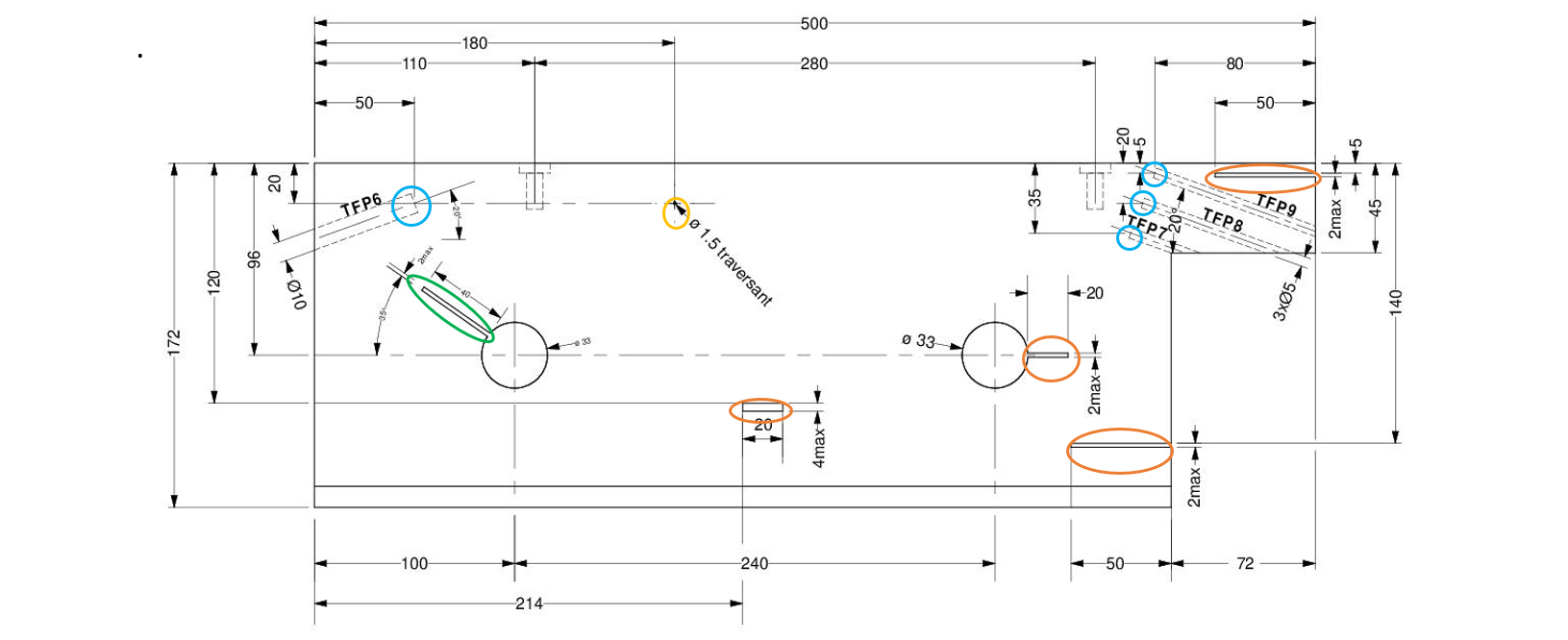
All defects are located in the axle of the rail
with: Transversal crack in blue, Bolt hole crack in green, Through hole in
yellow and Horizontal crack in orange.
1. Inspection principle:
The installation of a sliding system allows us to simulate an automated Ultrasonic Rail flaw detection. In regards to conventional ultrasonic probes, the inspection has been made using 3 different types of probes, which are 70°, 35° and a 0°. For the Phased Array transducer, the setting has been made to transmit simultaneously the 3 angles (0°, 35° and 70°). The receiving process is done in real time and data are processed separately in the same way as for conventional probe.
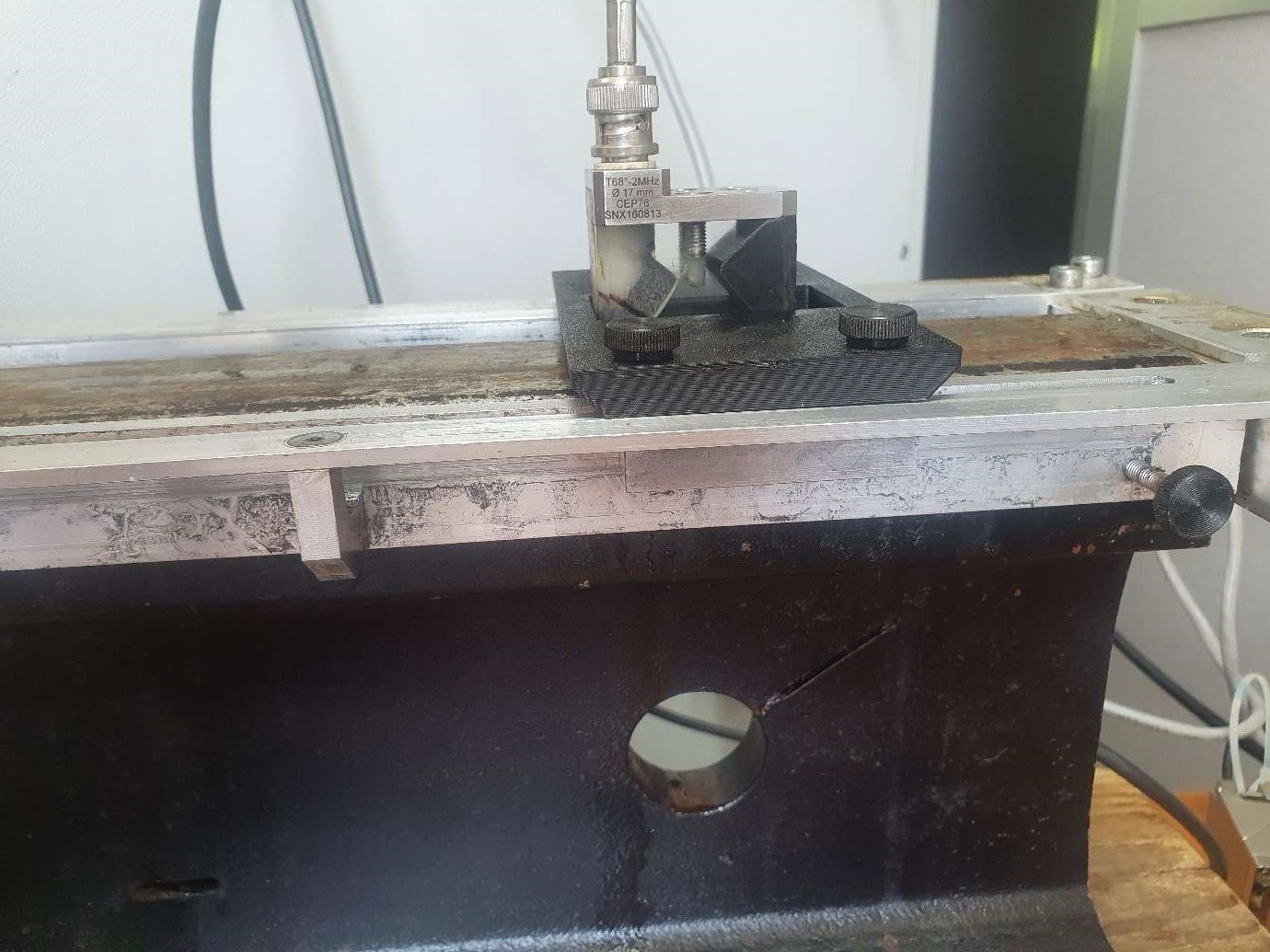
2. FAAST-PA brings flexibility and savings compare to conventional ultrasound for Rail flaw detection
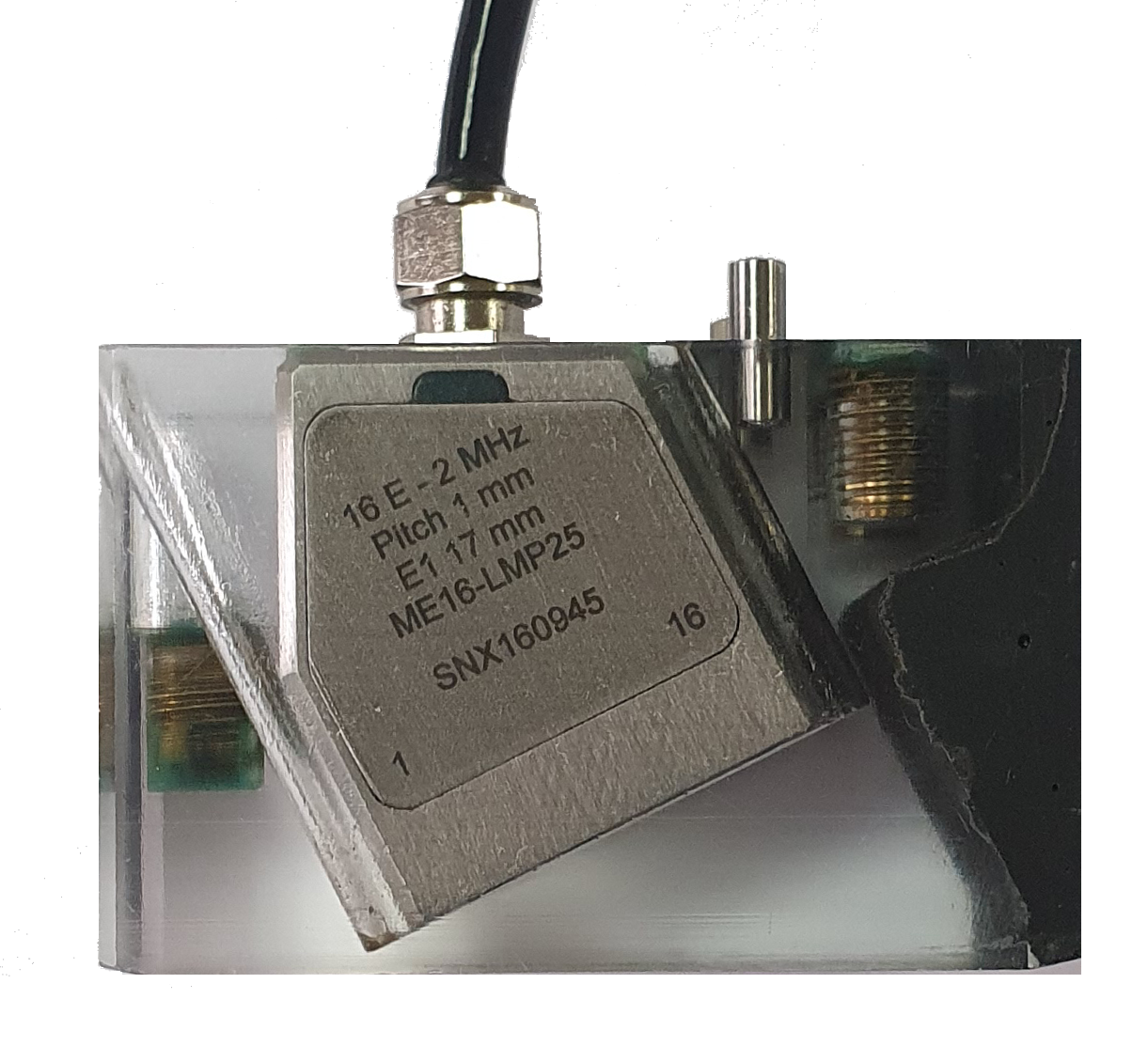
Last designed probe is a 16 elements probe, pre-oriented and having the same size as a conventional probe to easily use existing mechanics or be part of next projects. The phased array transducer combined with FAAST can generate up to 7 ultrasonic beams at the same time for flaw detection, between a range of 35° to 70°. An eighth angle at 0° shot is used in order to check coupling at each emission as well as looking for corrosion underneath the rail. Using such technology ensures an accurate ultrasonic testing of Railway track to find defects. All 7 angle beams are managed by computer control offering flexibility, avoiding mechanical orientation as with conventional probes. To resume, one phased array transducer can replace 7 conventional probes, saving on space and water, offering computer control of the 7 angle beams while having a good probability of detection at low and high speed for ultrasonic rail testing.
3. B-Scan imaging results between conventional ultrasound and Phased Array Ultrasonic
While it is understandable to be sceptical that one phased array transducer can provide same results as 7 conventional ultrasonic probes for Rail flaw detection, the following trials will demonstrate that it is achievable. The rail sample has the defects presented in fig. 1, and has been inspected first with conventional probes, then with a 16 elements phased array transducer. Hereafter is a B-Scan imaging of defects with probes looking forward:

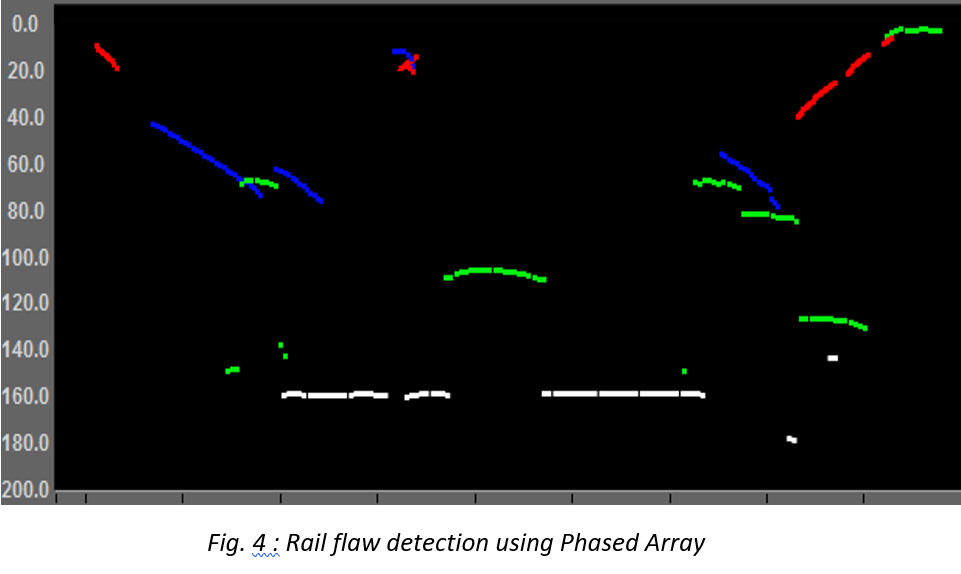
4. A-Scans results between conventional ultrasound and Phased Array Ultrasonic
The A-scans are all showing a good probability of detection using both technics, below images are showing acoustical results of Ultrasonic rail flaw detection. The left image identifies the targeted defect with a yellow circle, the centered image presents the A-Scan using conventional probes and right image the one with Phased Array transducer.
Ultrasonic inspection of Through Hole crack:

Ultrasonic inspection of Transversal cracks:




Ultrasonic inspection of Bolt hole crack:

Ultrasonic inspection of Horizontal cracks:




5. How FAAST-PA can be used and its advantages for Ultrasonic rail flaw detection
Whereas conventional ultrasound is widely used, a unique patented phased array instrument can bring high advantages by using a Phased Array probe able to generate multiple angles in a single shot and process the data in the same way of having multiple mono-element probes.
First, the capability of setting angles by computer control offers a high flexibility in system configuration and avoid mechanical orientation. The Phased Array transducer can be adapted to any type of probe holder as for conventional probes and Ultrasonic rail testing can be achieved at low and high speed. Secondly, as we drastically reduce the number of probes it saves water for coupling as well as number of spare parts. The above example showed results on defects located in the axis of the rail, however is not limited to since many other kinds of defects exist in real conditions such as: Vertical split head, Head web separation, Wheel burn, Upper fillet crack.
Economically speaking, other defects such Internal transverse or Shelling are inspected with offset probes, which could be done with conventional ultrasound to make a hybrid system.
Socomate International provides Ultrasonic equipment & software turn-key system for Ultrasonic Rail flaw detection, SOCORAIL. To find the right equipment and solution to your rail project, contact us today!